Comprehending Porosity in Welding: Checking Out Causes, Results, and Avoidance Techniques
As experts in the welding sector are well conscious, comprehending the reasons, effects, and prevention methods associated to porosity is critical for achieving robust and reputable welds. By delving into the root triggers of porosity, analyzing its detrimental effects on weld high quality, and checking out effective avoidance strategies, welders can improve their knowledge and abilities to produce high-grade welds constantly.
Typical Reasons For Porosity
Porosity in welding is largely brought on by a combination of factors such as contamination, improper protecting, and insufficient gas coverage throughout the welding procedure. Contamination, in the kind of dust, grease, or corrosion on the welding surface area, develops gas pockets when warmed, bring about porosity in the weld. Incorrect securing happens when the securing gas, frequently utilized in processes like MIG and TIG welding, is unable to fully safeguard the molten weld pool from reacting with the bordering air, causing gas entrapment and succeeding porosity. Additionally, poor gas insurance coverage, usually because of wrong circulation prices or nozzle positioning, can leave parts of the weld unsafe, allowing porosity to create. These factors collectively contribute to the development of voids within the weld, compromising its stability and possibly triggering architectural problems. Recognizing and attending to these common reasons are vital actions in stopping porosity and making certain the high quality and strength of welded joints.
Effects on Weld High Quality
The visibility of porosity in a weld can considerably jeopardize the total high quality and honesty of the bonded joint. Porosity within a weld produces spaces or cavities that weaken the framework, making it much more at risk to breaking, deterioration, and mechanical failure.
Furthermore, porosity can impede the efficiency of non-destructive screening (NDT) techniques, making it challenging to discover other flaws or interruptions within the weld. This can bring about considerable safety and security problems, particularly in essential applications where the architectural stability of the bonded parts is paramount.
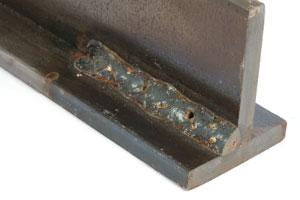
Prevention Techniques Summary
Offered the detrimental effect of porosity on weld top quality, reliable avoidance techniques are essential to preserving the architectural integrity of welded joints. Additionally, selecting the suitable welding parameters, such as voltage, current, and take a trip rate, can assist lessen the threat of porosity development. By including these prevention techniques right into welding techniques, the event of porosity can be dramatically lowered, leading to more powerful and much more trusted welded joints.
Value of Appropriate Shielding
Appropriate securing in welding plays an important function in avoiding climatic contamination and ensuring the integrity of welded joints. Securing gases, such as argon, helium, or a blend of both, are frequently used to protect the weld pool from reacting with components in the air like oxygen and nitrogen. When these reactive components enter contact with the warm weld pool, they can create porosity, causing weak welds with decreased mechanical buildings.

Insufficient securing can lead to numerous problems like porosity, spatter, and oxidation, endangering the structural stability of the bonded joint. Adhering to proper protecting techniques is important to generate top notch welds with minimal problems and make sure the durability and reliability of the bonded elements.
Surveillance and Control Methods
How can welders effectively monitor and control the welding procedure to make certain optimum outcomes and prevent defects like porosity? By constantly keeping track of these variables, welders can recognize discrepancies from the optimal problems and make instant adjustments to prevent porosity development.

In addition, carrying out correct training programs for welders is necessary for keeping an eye on and regulating the welding process properly. What is Porosity. Enlightening welders on the significance of keeping constant parameters, such as correct gas securing and travel speed, can assist avoid porosity concerns. Routine see this website assessments and accreditations can also make certain that welders are skillful in tracking and regulating welding procedures
Moreover, the use of automated welding systems can boost tracking and control abilities. These systems can exactly control welding criteria, reducing the likelihood of human error and making certain consistent weld top quality. By incorporating advanced surveillance modern technologies, training programs, and automated systems, welders can effectively keep an eye on and regulate the welding procedure to minimize porosity problems and achieve premium welds.
Verdict

Comments on “Comprehensive Guide: What is Porosity in Welding and Just How to avoid It”